Pedal box cover
April
2001
This was originally some weird plastic thing. Held together with duct-tape.
Mmm... nice.
So I made a new one from some Ali sheeting I had lying around. I first made cardboard templates of the 3 pieces (2 sides and a front/top). I then made the required cutouts in the cardboard pieces so that they cleared all the obstructions etc.
I then used the templates to mark up the Ali sheeting using a permenant marker. Once the main outline was transfered I added extra shapes which form the "flaps" between the panels.
Once this looked ok I cut the Ali panels out. I cut using a combination of a pair of
tinsnips, a metal chisel and a dremel. I then filed off the edges using a grinder to ensure there are no spikey bits.
I bent the sheets to get the flaps etc using a workbench with two pieces of steel angle-iron to give nice hard edges to press up to.
Trial fitting of the bits is required at each stage.
When I was happy with the fit of all the panels I put them in position, secured it all solid with duct tape and then drilled the existing holes through from the pedal box. I then secured the pedalbox to the cover with self-tapping screws.
You can then go around all the "flaps" and drill/rivet them together.
When done it should be reasonably well sealed. For extra sealing power a bead of silicon sealant was run on the inside of the edges of the cover to act as a rubber'y cushion.
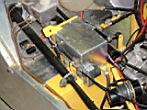 |
Pedal Box cover in position |
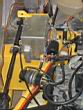 |
Pedal box cover from the other side, note the revised mounting of the bike engine fuel pump too - much more solid now. |
Aeroscreen
May
2001
The Striker windscreen is an awkward beastie. It is raked at a mad angle
that makes getting at the dashboard tricky. It is also heavy (6.5Kg) and
is useless without the ugly sidescreens. Take away the rest of the
windscreen gear and you can save 9Kg.
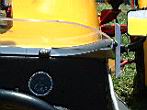
|
For a Striker Aeroscreen I turned to Peter Carr.
He has a home-made screen shown in the photos here.
He is also
experimenting with funny side flaps and has also made his car into a
dukes-of-hazard type with fully enclosed sidescreens!
|
|
For my screens I opted for something a little
different.
I wanted to retain the same mounting holes as the windscreen uses, and
drill no new ones at all. A swappable setup.
To do this I made a frame from 20mm Ali Box section. I put this
down the side of the screen, and marked where I wanted the 90degree bend
to be. I then cut a "V" shape for this with an angle
grinder, making sure I didn't completely sever the tubing. See the
photo. I then filed the edge clean and GENTLY bent the thing into a
right angle.
Position this across the windscreen edge, secure with duct tape and
work out where to put the next bend. Be careful as you need to allow
for the material thickness in the bend radius.
One made the surround is then drilled to match the existing mount holes
(2 per side 8mm for me).
Once secure make yourself an aeroscreen template. I used some
cardboard. it took two attempts to get the curves into the bodywork
correct. I opted for a 4" high screen which from the Stoneleigh
show seemed to be the standard for all seven style cars.
I had a local plastics company (http://www.edplastics.co.uk) use my template to make the
screen. Here you can see it fitted after I have drilled a lot of
holes (for self tappers into the Ali frame).
I left the packing covering on to help prevent scratches. |
|
The completed screen with and without the
bonnet in place.
The screws are stainless self-tappers. Use washers to help
prevent cracking the screen when you tighten the screws. |
Seating
May
2001
I was never 100% comfortable in the car pre engine install. Being a short-arse
I had to move the seat forward and I always felt like I was sitting in the boot.
I had a wooden board behind the seat but this was not ideal!
I wanted to have the seats adjustable and raise them up a little. I
looked at new seats but to be honest the cars condition really doesn't warrant
posh new expensive seats. I have a couple of GRP bucket seats but they are not a
pair and are pretty uncomfortable to sit in (at least for me).
So I elected to try to use the existing pair of two piece seats. I realised
that rake adjustment can be obtained by linking the two pieces together (seat
back and seat cusion), and hinging them. I sketched some ideas and came up with
a deckchiar type adjustment with a support stay coming out the back to prop the
seat up. For material I used some steel hinges, some Ali box section, and some
steel (3mm) strip.
The first attempt actually used Ali strip for the rear seat back rails. These
bent very easily though so I ditched them and used more Ali box.
The completed seats are quite strong (at least for me) and the back can be
adjusted to be at 3 different rake angles. The seat bottom rails were cut to the
right length to push the seat forward enough for me, and raise the seat by
1". This is now pretty much the perfect driving position for me (I think).
Bodywork
April
/ May
2001
The original car was finished in a maroon (Bordeaux) gelcoat. The owner previous to me was an artist and hated the
colour. So he started to paint it. But he didn't finish. So the car has a maroon rear, a yellow bonnet and green cycle wings! It looks like a Harlequin!
With this in mind I wanted to tidy it up. Although I'd really like it bright yellow I decided to keep the easy bit (the rear) and paint/change the rest to match.
I
checked the bonnet fit and found it was hitting my header tank and my
thermostat. I moved the header tank down about 7mm by drilling extra holes
in it. I undid all of the water pipes around the thermostat and took the
thermostat apart. The top-pipe is an overflow and I found that I could
move its position easily and have the pipes a little neater.
Old exhaust
hole - patchup
Old air-filter hole - patchup
|
May 2001
Here we have the preperation of the hole that used to have weber DCOEs
sticking out.
A curved hole needed to be patched.
The technique is:
- get some wire mesh and put this over the outside of the hole
- secure the mesh with some self tapping screws (drill pilot holes
first or you'll crack the GRP)
- Use duct tape to secure the edges of the mesh
- Line the inside of the mesh with parcel tape (shiny side up).
This will be our "release agent" for the GRP
- secure the outside with more duct tape.
- Prop the bonnet on its side so that it is not stressing the hole
Then cutout the fibre matting layers and position neatly at one side.
|
|
Mix some resin and hardener and layup the job. Ensure
that you overlap on the inside to give the panel strength. |
|
Magic.
The outer stuff removed - we are left with a nice GRP panel. Some
sanding and filler and it will look like new (yeah right!). |
|
The next stage is to clean off the rough edges where the
fibreglass comes through. An angle grinder with a sanding flap disk
is ideal but be careful not to take off too much!
Then use a layer of P38 filler across the whole section. Try to
get it into the nooks and crannies and don't use too much - or it will
take longer to get off. Do this a few times and you should start to
fill all the holes. Sand off and do again. When you think the
holes are filled get some cellulose stopper - this is a facecream
consistency finishing filler. Use this to cover the repair.
Use a finer grade of sandpaper to get the filler down. Wet n dry 400
is good. Repeat the stopper application as required.. |
|
The panel should now be pretty well covered. Now try
some spray putty over the whole thing. This will show up the last
blemishes. If you are going for concourse looks then you just have
to keep going over and over until it is right. My car is not a
looker so I finished after a few loops round. Once sanded with fine
wet n dry (1200) it can be undercoated and then painted. |
Registering the car with the new engine
April
2001
You need to tell DVLA the new engine number and capacity (to get the cheaper
road tax!).
Some people have had trouble with this so I elected to be pretty
thorough. I completed the form and enclosed the following documents:
- A copy of the engine receipt, showing the engine# on the receipt.
- Two photos, one of the new engine#, and the other of the completed
installed engine, alongside the bonnet with number plate.
- A spec sheet on the engine from Yamaha's website.
This did the trick and 2weeks later I received a new document with 998cc and
the new engine#.
Other Tips
|
Feb
2001
A cheap mobile toolbox solution.
Available from Argos for about £30. Castors are a bit flimsy
and the whole thing wobbles - but you get what you pay for! I may
make a steel frame for the drawers one day. |